Guideline for Using Composite Materials for Pipeline Repair
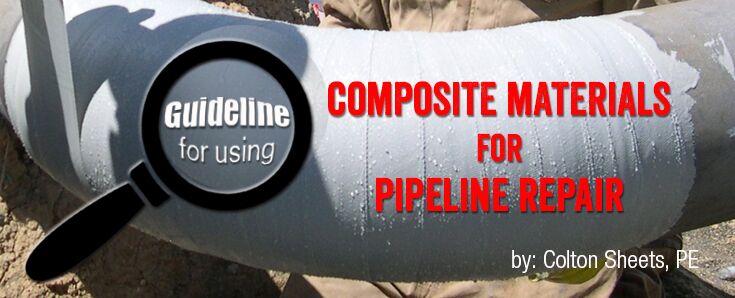
Composite Materials for Pipeline Repair
Numerous public and private studies completed over the last 20 years have investigated the potential benefits of using composite repairs for structural reinforcement of pipelines. These studies have demonstrated that when composite repair systems are designed and installed correctly, they can restore a pipeline’s structural integrity for a wide range of anomalies and applications—even to an extent that the performance level of the damaged pipe is equal to that of the original pipe.
The studies have also shown that a poorly designed or improperly installed composite system will provide little to no benefit. This means that acceptable performance of a composite repair is critically dependent on three primary components: (1) analysis of the anomaly to be repaired, (2) a proper design, and (3) correct installation of the repair system.
Much of the research associated with composite repair systems has focused on corrosion in high-pressure pipelines. However, recent research has also been conducted to evaluate the reinforcement of a wider range of pipeline anomalies including wrinkle bends, branch connections, elbows/bends, planar defects, and girth welds.
Pipeline Repair Considerations
Stress Engineering Services has developed a methodology to assist pipeline operators in evaluating the severity of pipeline anomalies as part of their overall integrity management programs. This methodology—the Engineering-Based Integrity Management Program (EB-IMP®)—integrates existing knowledge, analytical techniques, experimental methods, and engineering rigor to develop tools to ensure pipeline integrity.
A similar approach can be used in evaluating pipeline repair methodologies. As the complexity of the repair increases, so should the level of evaluation. Having a set of specific requirements that can be enforced through documentation and inspection is critical to ensuring proper implementation of composite repairs.
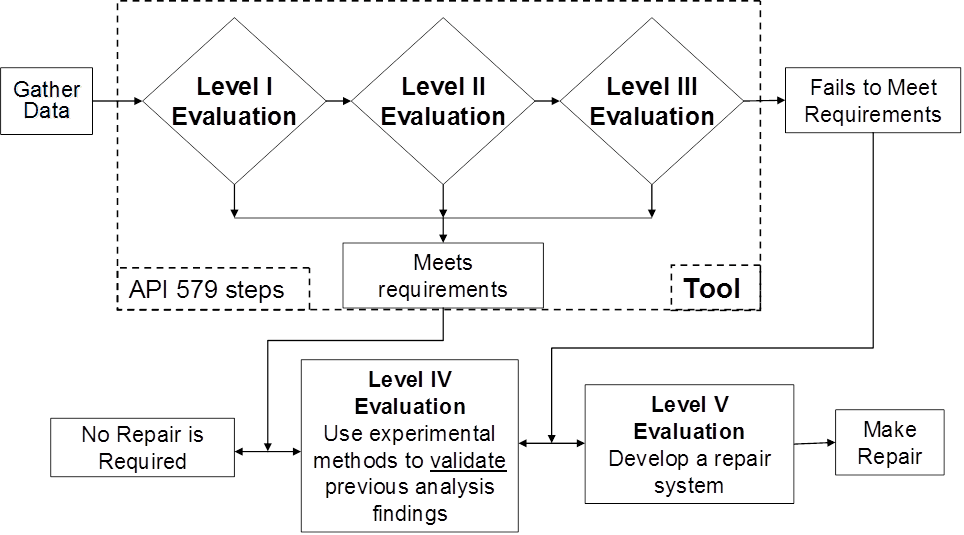
Developing an Optimized Repair Solution
It is essential that composite repair end users is to know the critical aspects required to achieve an optimized repair solution so that processes can be developed that ensure all components are appropriately addressed.
The flow chart outlines key elements of an optimized repair solution.
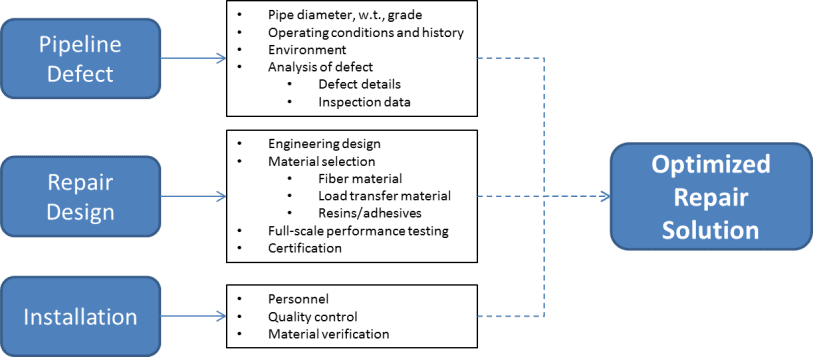
ASME PCC-2, Repair of Pressure Equipment and Piping, Article 4.1, Mandatory Appendix 1, contains a two-page
“Component Repair Data Sheet” that is an ideal reference for ensuring that all facets of the repair have been completed.
Assessing Pipeline Anomalies
Before designing and installing a composite repair, there must be a basis for determining the repair requirements. An anomaly targeted for repair must be characterized in terms of extent and severity to determine its impact on the integrity of the pipeline. For example, essential data to assess corrosion includes pipe diameter, wall thickness, and material grade, as well as corrosion depth and length. Standards and guidance documents such as API 579/ASME FFS-1, ASME B31G, or BS7910 are typically used to perform the required calculations for corrosion assessment. As part of this assessment, the decision must be made as to whether the anomaly is repairable.
Once the severity of the corrosion has been assessed, the repair requirements can be determined using available standards such as ASME PCC-2-2015 (Part 4 Nonmetallic and Bonded Repairs, Section 3 Design). Before a composite repair is designed, the pipeline defect must be properly evaluated to ensure that all facets of operation are taken into consideration. ASME PCC-2 addresses this by including a list of important questions to be resolved in the “assessment” process.
Assessment Process Questions:
- What is the required lifetime of the repair?
- What measurement details are available for the features to be repaired?
- What loads can be expected, including external bending moments and axial loads?
- What is the pipeline’s operation history including the range and frequency of pressure cycles?
- What are the expected ambient temperatures of the soil/water/atmosphere in the vicinity of the repair, as well as the maximum operating temperature of the pipeline?
Designing and Installing a Composite Repair System
After the severity of the anomaly is evaluated, the composite repair system can be designed. It is essential that a composite system used to repair pipelines have the necessary documentation to demonstrate its worthiness. Repair systems should have third-party certification from a reputable engineering firm that has evaluated the system based on the requirements of the ASME PCC-2 (or ISO 24817) standard. For repairs other than corrosion, the system should be subjected to full-scale destructive testing to ensure that an adequate level of reinforcement can be provided. This should also apply if external loads (e.g., axial and bending) will be acting on the composite repair. The effects of static and cyclic pressure should be considered in the design of any repair.
The final stage of the process involves actual installation of the repair. Properly installing composite materials is an essential element of the repair process. Failure to install the repair properly creates a condition where substandard performance can be expected.
Special points of interest:
• Composite repair research has included a wide range of pipeline anomalies (corrosion, dents, cracks, girth welds, wrinkle bends).
• There are three components of a successful repair: anomaly assessment, repair design, and repair installation.
• Documentation of the three components is critical to maintaining integrity.
Designing a System
Important considerations and questions to address when designing a composite repair include:
- What is the elastic modulus and short-term tensile strength of the composite material system? Factors that affect performance of the composite material include fiber type, matrix material (i.e., resin), and fiber orientation.
- Are there chemical compatibility issues between the composite materials and the external environment or fluids that may come in contact with the repair?
- Has an appropriate filler (i.e., load transfer) material been selected and tested?
- Is material property data, including filler and composite fiber material, available as a function of temperature? Having data on the matrix resin alone is not sufficient for applications where conditions exceed room temperatures.
- Has the repair been full-scale tested using the conditions it will experience in service?
- What documentation has been provided from the composite manufacturer/supplier?
- Are quality-assurance methods, including traceability and tracking, in place to ensure that what has been designed is delivered to the end user?
Installing a System
Listed below are several key questions that should be addressed when composite materials are installed on pipelines:
- Has the pipeline been properly exposed and has the surface been abrasively blasted to the manufacturer’s recommendations?
- Have the personnel making the repair been properly trained?
- Have the correct materials been selected and installed according to the installation procedure?
- How much cure time is required before the line can be placed back in service?
- Are there service temperature limits during installation?
- What measurements can be taken to ensure that all adhesives and resins have cured properly (e.g., hardness tests, etc.)?
Final Thoughts
In summary, a good rule for any pipeline operator is that a composite repair system must demonstrate that it meets the requirements of industry standards such as ASME PCC-2 and/or ISO 24817 before being used to repair a pipeline anomaly. Composite manufacturers should be able to produce documentation from a third-party organization demonstrating their compliance with these standards and the required material and performance properties. When reinforcing anomalies more complex than standard external corrosion, it is essential that testing be conducted to demonstrate that adequate performance levels can be achieved. The same principle applies to applications in previously untested environmental conditions or load conditions outside of static internal pressure.
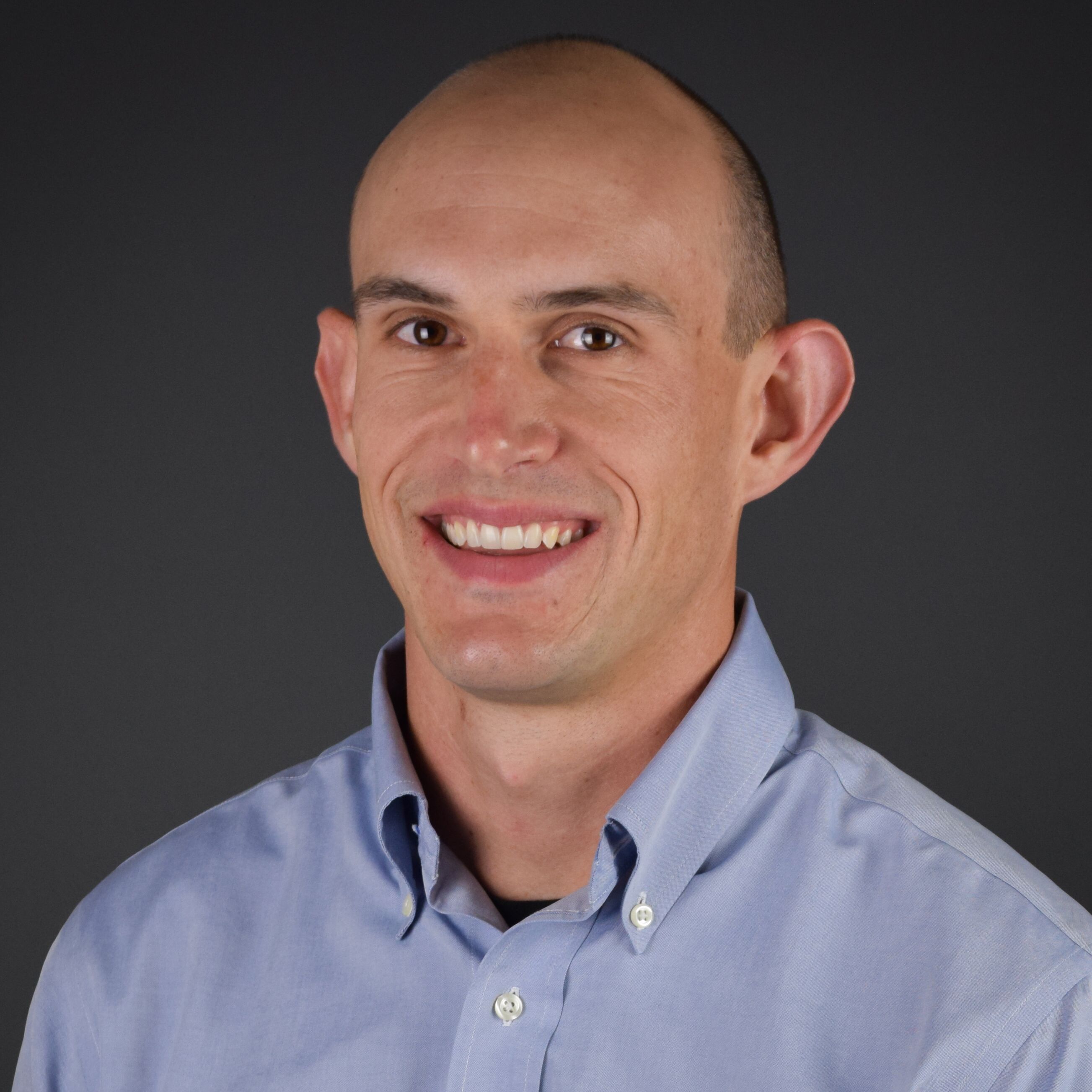
Colton Sheets, PE – Associate, Houston Office
Colton is an integral part of our Midstream Group where he utilizes his experience with testing and analysis of both onshore and offshore components and pipelines. He is also active in industry organizations including ASME PCC-2 – Repair of Pressure Equipment and Piping and is a registered Professional Engineer in the State of Texas.
Leave a Comment
You must Register or Login to post a comment.