Accelerating the Aging Process: Pressure Cycle Testing to Improve Product Design, Development, and Qualification

By: Matthew W. Sanders, PE
Testing is critical in developing and manufacturing high-quality and high-performance products, since it can provide valuable insights into a product’s strengths and weaknesses. This allows manufacturers to make informed decisions about design, materials, and production processes. One type of testing that can accelerate the qualification process and simulate years of service conditions in a short amount of time is pressure cycle testing.
In pressure cycle testing, a product or component is exposed to a series of cyclic pressure loads. This simulates real-world conditions in products such as medical devices, aerospace components, industrial control systems and automotive/transportation parts, and can be used to evaluate a product’s performance over time.
Pressure cycle testing is a powerful tool in the product development process that can help streamline and reduce costs.
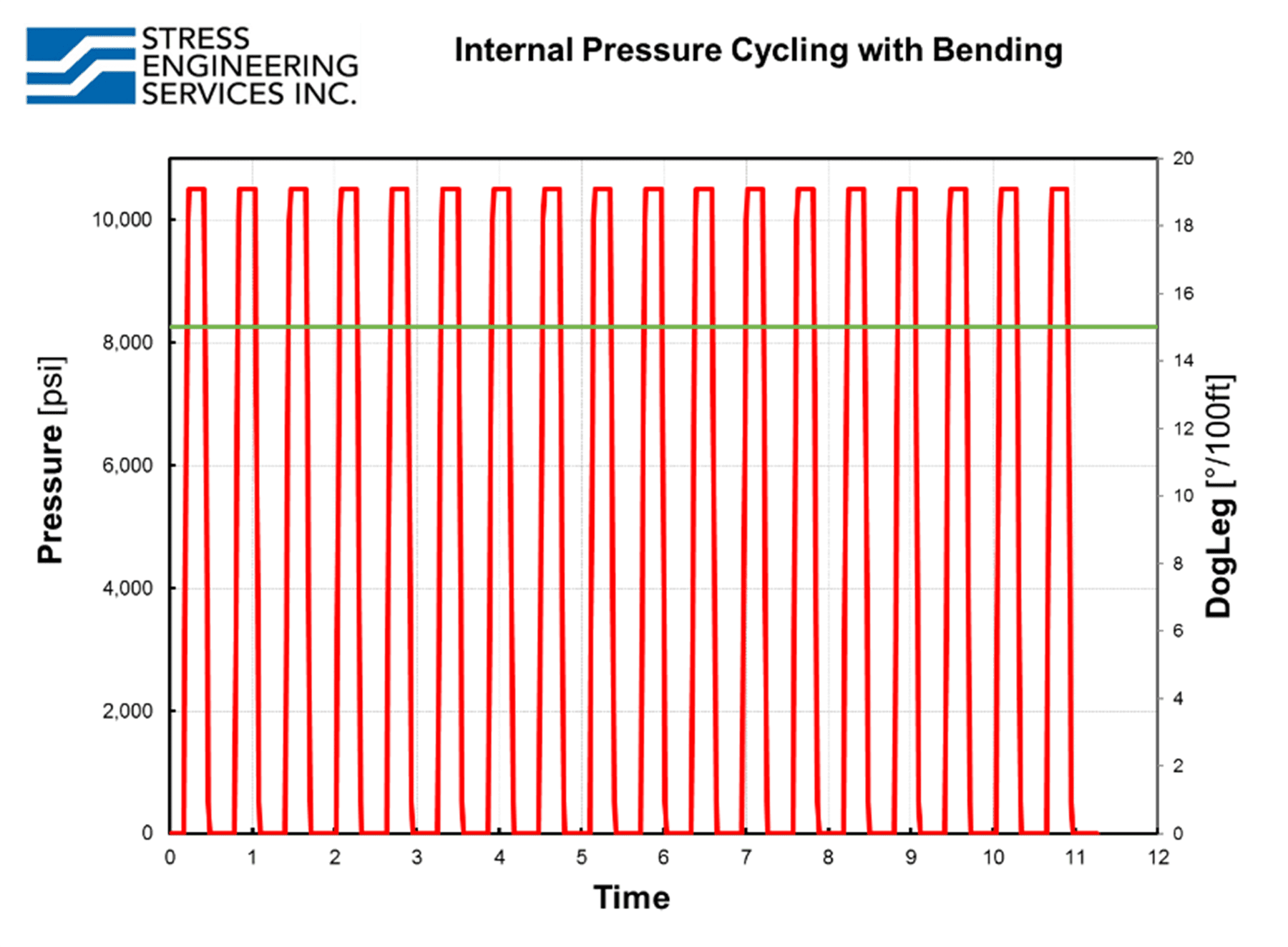
Figure 1: Example Pressure Cycle Test Data
Stress Engineering’s test lab has completed complex cyclic pressure testing programs with challenging parameters such as; sine and square wave pressure profiles, up to approx. 30,000 psi, 0.5Hz frequency, or over 500,000 cycles. Some of the benefits that this type of testing can provide include:
- Faster time to market: By simulating real-world conditions in a controlled laboratory environment, pressure cycle testing can help identify potential issues and optimize product performance earlier in the development process. This can help speed up the time it takes to bring the product to market.
- Improved product reliability: By testing a product’s performance under different conditions, pressure cycle testing can help identify potential weaknesses and improve reliability. This can help reduce the risk of product failures and costly recalls, which can save significant time and resources in the long run.
- Better product design: Pressure cycle testing provides valuable data that can be used to optimize product design and reduce manufacturing costs. By improving product design, the need for subsequent modifications and re-designs can be avoided.
- Increased customer satisfaction: Pressure cycle testing can help ensure that products perform as intended and meet customer expectations, boosting customer satisfaction and reducing the risk of lost business due to product failures or performance issues.

Figure 2: Pressure testing setup for multiple pressure zone testing.
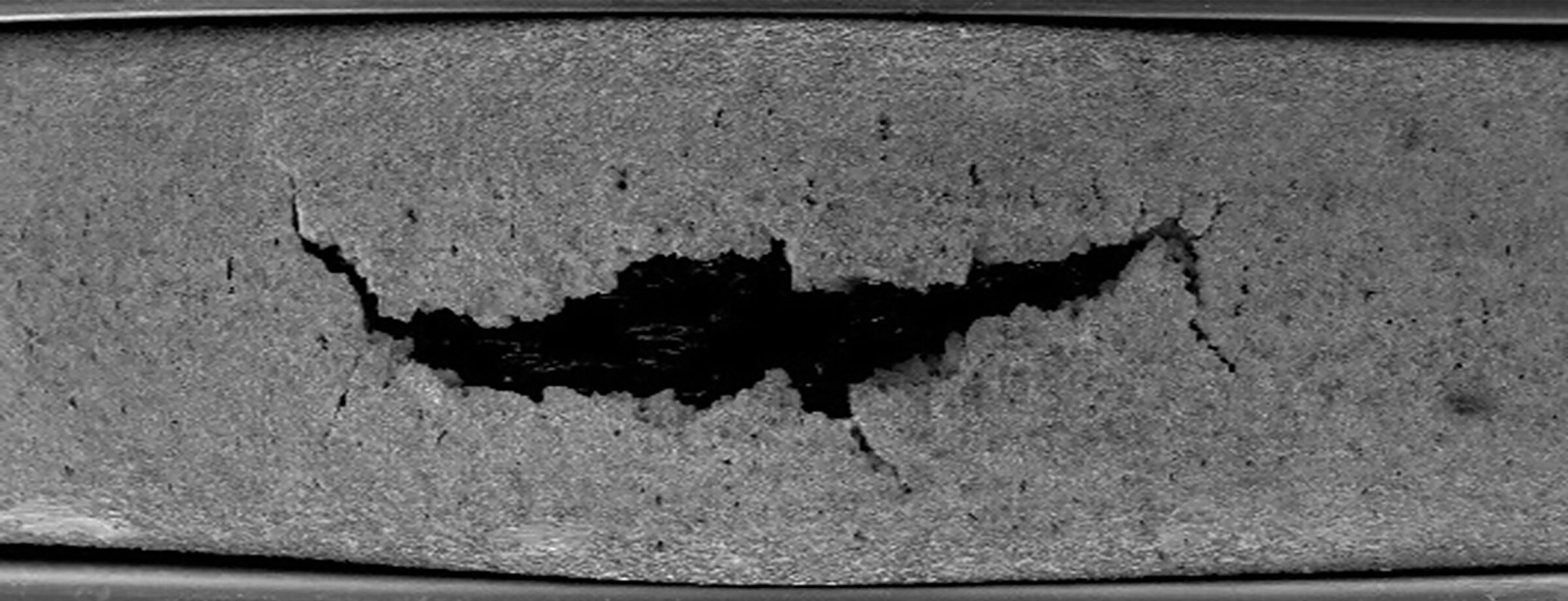
Figure 3: Test article failure from pressure.
Real world applications
Many products are subjected to pressure fluctuations in the field, which can have a significant impact on its performance, reliability, and safety. For example, a valve in a refinery piping system may experience rapid pressure fluctuations as fluid is pumped through the system. Similarly, a hydraulic cylinder may experience cyclic pressure loads as it extends and retracts. The United States’ national pipeline system is a critical piece of infrastructure that experiences pressure cycles regularly, which can lead to fatigue induced failures. By testing these products under controlled conditions, key stakeholders can gain a better understanding of how they will perform in the field.
One of the key benefits of pressure cycle testing is that it allows manufacturers to identify potential problems before a product is released to the market. By exposing a product to cyclic pressure loads, manufacturers can identify issues such as leaks, cracks, and structural failures. This information can then be used to make improvements to the design, materials, or production process.
Another advantage of pressure cycle testing is that it can be combined with other applied loads to simulate real-world conditions more accurately. For example, a product may be subjected to pressure cycles while also being subjected to temperature changes (both hot and cold), tension and compression loads, bending loads, and harsh environments. This combination of loads allows manufacturers to evaluate the total impact of real-world conditions on a product’s performance.
In some cases, end users or manufacturers may also want to perform impulse pressure cycle testing. This type of testing involves exposing a product to rapid pressure cycles. The goal is to evaluate the effect of impulse loads on the product and identify potential failure points. This type of testing is particularly important for products that are subjected to rapid pressure fluctuations in the field, such as hydraulic systems and aerospace components.

Figure 4: Digital Image Correlation (DIC) data taken during pressure testing.
Gathering meaningful data
Pressure cycle testing can be a time-consuming and expensive process, and it is important to perform it correctly and accurately to obtain meaningful results. Some of the challenges involved in performing pressure cycle testing include:
- Equipment: High-pressure testing equipment can be expensive, and the cost can be a significant barrier.
- Testing Time: Pressure cycle testing can take a long time, especially for complex components and systems with large volumes. This can delay the product development process and increase costs.
- Accuracy and Data Collection: Collecting accurate and reliable data during pressure cycle testing can be a challenge. This requires specialized knowledge and equipment, as well as a well-designed testing protocol to minimize parameter deviations and capture proper data.
- Environmental Factors: Environmental factors, such as temperature and ramp/bleed rate, can have a significant impact on the results of pressure cycle testing. It is important to carefully control these factors to obtain accurate results.
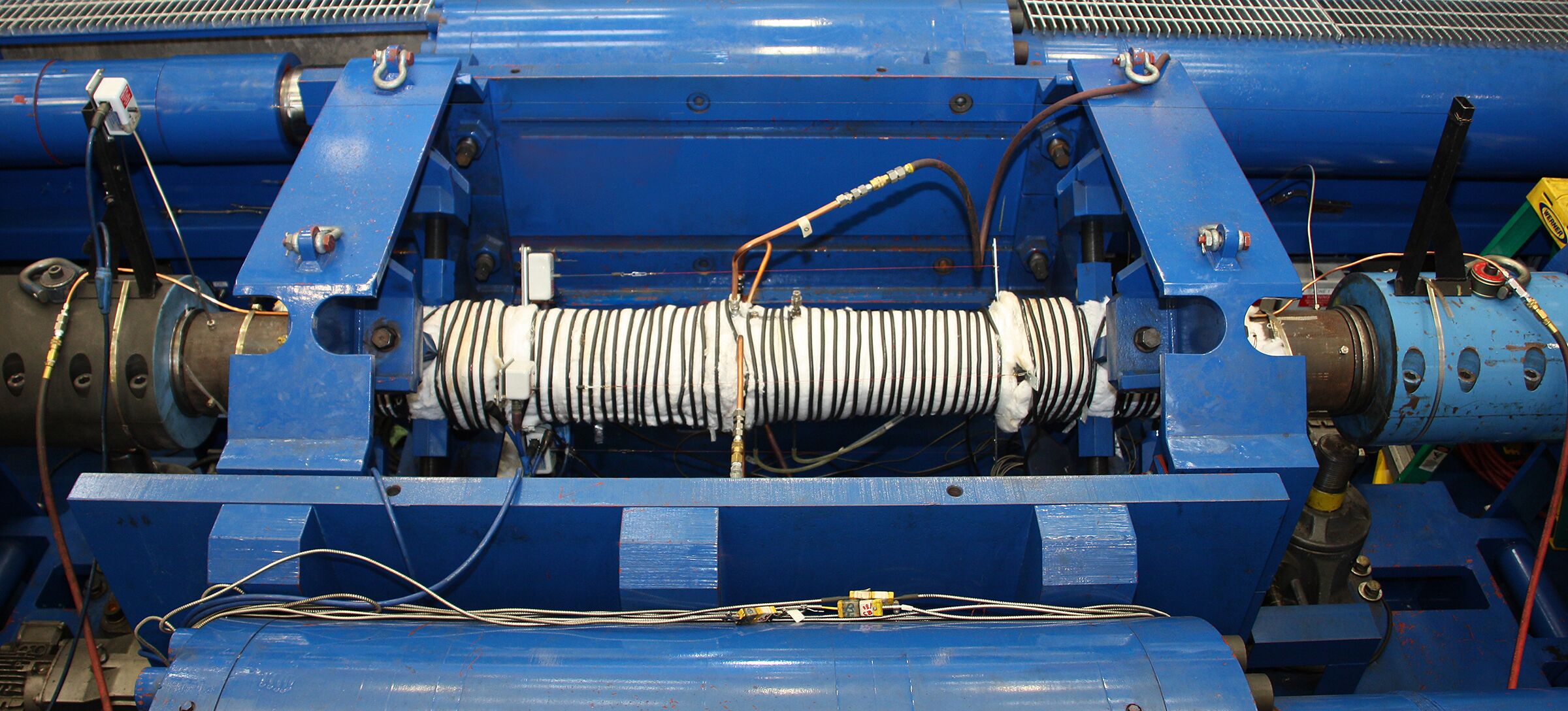
Figure 5: One of Stress Engineering’s Combined Load Test Cells setup for pressure, axial load, and temperature testing.
To overcome the challenges of pressure cycle testing, it is important to work with a reputable testing laboratory, such as Stress Engineering Services that has the expertise, equipment, and facilities to perform this type of testing accurately and efficiently. The laboratory should have a proven track record of delivering high-quality results and should be able to provide customized testing services to meet the specific needs of a product or component.
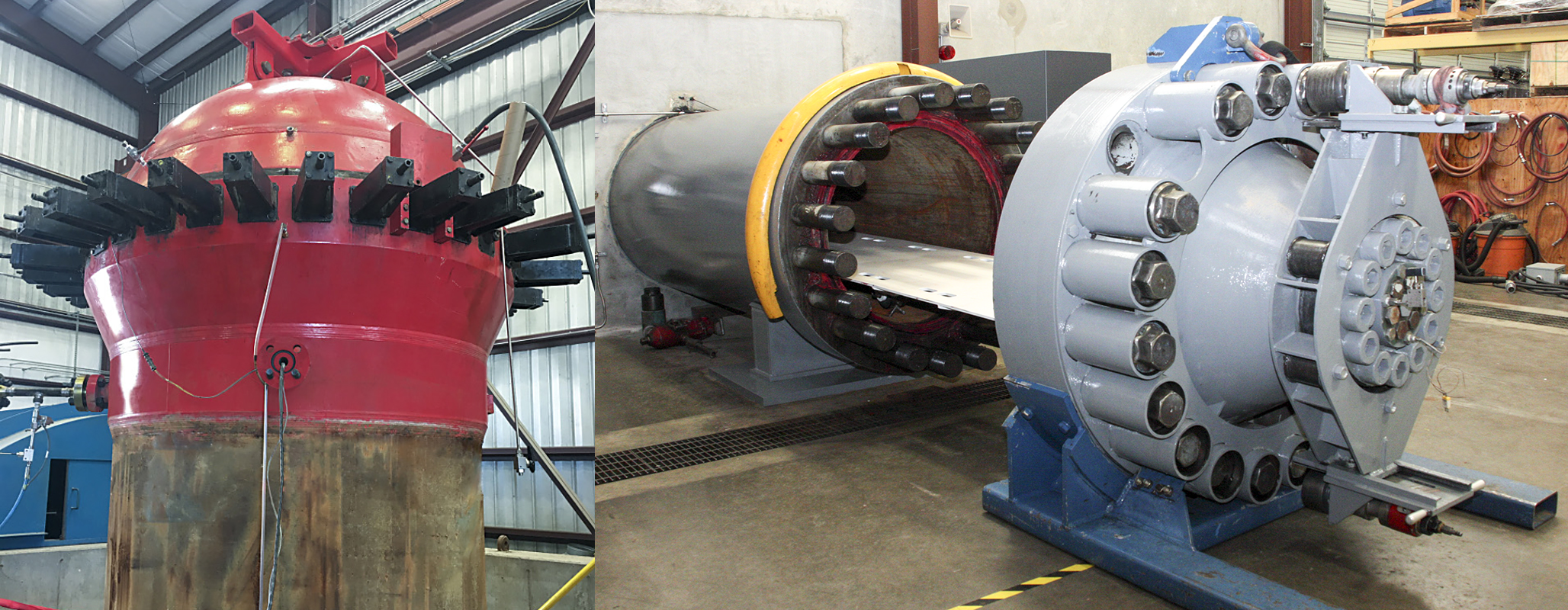
Figure 6: Some of Stress Engineering’s external pressure testing systems.
Summary
Pressure cycle testing is a valuable tool for manufacturers and end users looking to understand and improve the performance, reliability, and safety of their products. By simulating real-world conditions, stakeholders can identify potential problems before a product is released to the field and make informed decisions about design, materials, and production processes. Whether the goal is to test valves, pumps, or aerospace components, pressure cycle testing is an essential component of a comprehensive product development and qualification program.
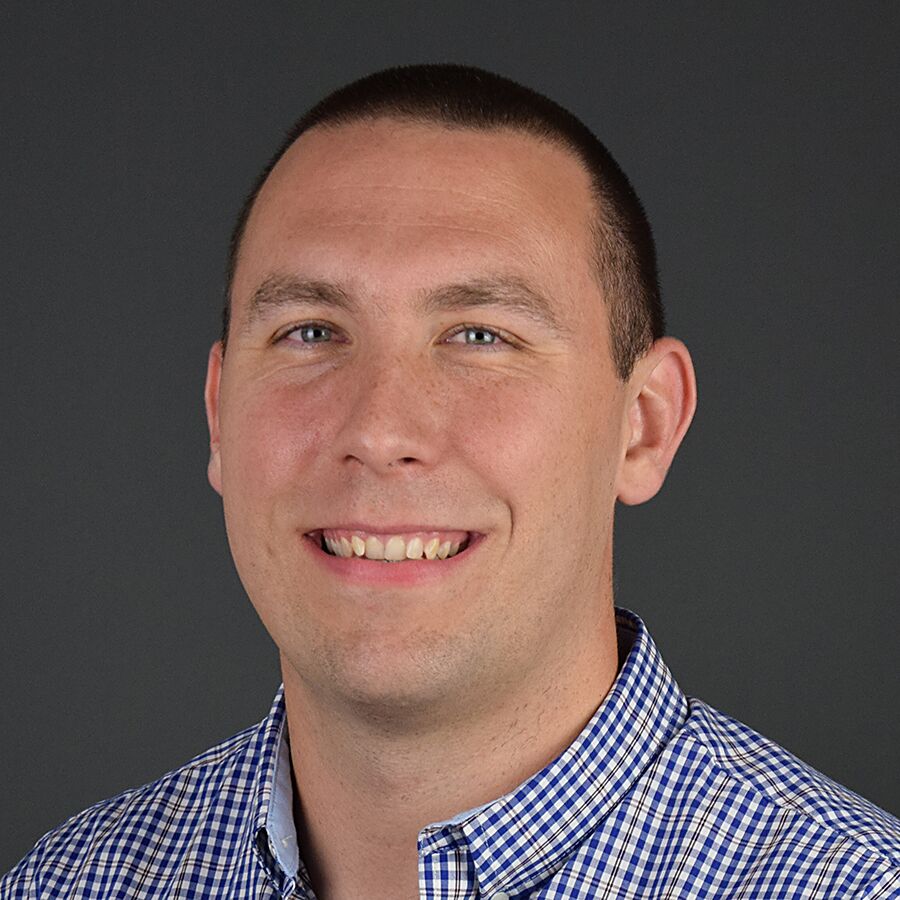
Matthew W. Sanders, PE – Principal, Houston Office
Matt specializes in the design and implementation of test programs including fixture design, project management and data analysis. He is also involved in downhole tool and screen mechanical testing, OCTG connection testing, ISO 13679 and API 5C5 testing, as well as the design of testing fixture to validate riser connection quick disconnect flanges under axial load and bending. In addition, Matt is involved in the design and implementation of qualification test programs including using advanced techniques to enhance finite element analysis of additively manufactured parts.
Leave a Comment
You must Register or Login to post a comment.