The Cost of Shipping… Air?

About four years ago, when my colleague and I were visiting the R&D packaging facility of a major snack food company, we noticed that a packaging engineer was manually filling a newly developed chip product into a clear plastic tube repetitively and taking the fill height measurements by hand. Out of curiosity, we asked what the test was for, and he told us that this was the test procedure to determine the size of the flexible bag for a soon-to-be-launched new chip product. Understanding the limitation of this test method, the packaging engineer compared the test data with the historical data of different stock keeping units (SKUs) in the company’s database and applied an experience-based safety factor to derive the final bag size for the company’s production vertical form fill sealing (VFFS) machines.
The costly by-products of volume
The snack flexible packages on the market today, such as, potato chips, pita chips, taco chips, tortilla chips, etc. are typically sold by weight, that is, the packages need to fulfill the label claims by weight. However, the size of the package is determined by the overall volume of the products. The determination of the overall volume of a given product weight is not inconsequential. The volume is a function of chip broken rate, chip size distribution profile, bag width, bag film gage and material, production line speed (bag/minute), VFFS machine type, etc. The packaging engineer explained that, in order to minimize the risk of potential seal contamination-induced leakage, the bag size is required to be bigger than what it should be. In practice, this means more air (fewer chips) in the finished goods. For snack packages, the shipping trucks are often cubed out by volume (not by weight). Energy is wasted in shipping as a result of excess air in the package.
Better bagging, not bigger bagging
So, we started to wonder… what if there was a simulation technology that could be appropriately adapted to the bag size determination and chip filling process, which could ultimately make chip bag filling more sustainable, i.e., capable of shipping less air? An appropriate simulation technology could help the industry by replacing the labor-intensive test process we witnessed, improve accuracy throughout the chip packaging process and reduce overall waste.
The Stress Engineering team, therefore, set to work developing a flexible chip bag filling simulation to enhance sustainability in product distribution. Bag size determination was carried out by using a virtual simulation of the VFFS chip filling process, where the potential influential attributes, such as, chip broken rate, chip size distribution profile, bag width, bag film gage and material, production line speed (bag/minute), VFFS machine type, could be modelled and their impact on the bag size quantified.
The bag filling simulation, which focused on the funnel/forming tube, bag and randomized falling chips in the funnel, was progressed in three cases:
Case # 1: Filling whole chips into a round plastic tube as the one used in the lab test
Case # 2: Filling whole chips into a flexible bag
Case # 3: Filling mixed whole and broken chips into a flexible bag
Pita chips (triangular shapes) were used for all three stages of the simulation. The whole pita chips have an equal length of the triangular side of 2 inch while the broken ones are ranged from 1/6 to 5/6 of the whole chip in weight. A total of 200 to 300 chips were modeled depending on the modeling stage (whole or mixed whole and broken chips). The total weight of the filling pita chips maintained at 22 oz. throughout. This was for a party size chip bag (approx. 9 x 15 inch bag). The filling process was simulated 100 times with different and randomized initial chip falling positions and orientations to capture the statistical variations of the chip settling height in the bag. The output of the each of the three simulation cases resulted in a histogram plot of the chip fill heights from repeated filling process.
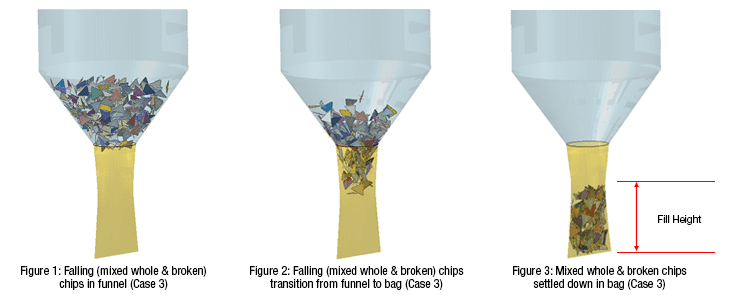
Findings summary
The results of the simulations of the three cases were interesting (Table 1).
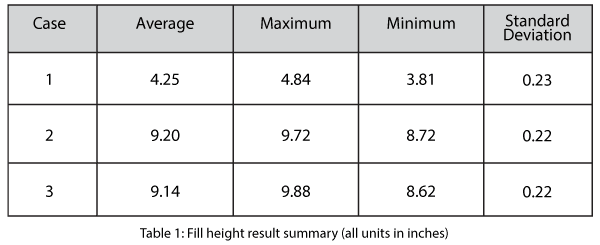
Although it could be expected that the flexible bags should have much higher fill height than the round plastic tube, the higher maximum fill height of the mixed whole and broken chip case than the whole chip case was a surprise. This might be due to the limited filling repetition and randomization performed in the test. It is noticed that the average fill height is reduced with broken chips included in the simulation. This is consistent with the lab test observations. From the animations of the filling simulations, the dynamics responses of the chips, bag and VFFS interactions appear to be realistic and adequate. The simulation technology is commercially viable to be scaled up in handling the actual bag filling process with more complex shapes of chips and more filling repetitions, to cover tail end of the distribution and increase confidence level.
Future outlook
The ultimate goal of this work is to simulate the actual bag filling process for both pillow and stand-up bags for various shapes of chips and snacks produced on different machines. This is not only for bag size optimization, but also for filling process optimization (line speed, etc.). Currently, we are working on expanding the model, accounting for variations including different shaped chips, different packaging film materials and the use of stand-up pouches. One of the key elements of the future development is the full automation of the simulation process, with the possibility to incorporate machine learning and artificial intelligence technologies to speed up the optimization process with minimum human interventions.
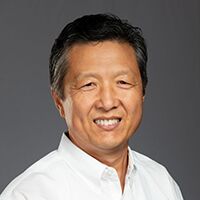
Jay Yuan, PhD, PE – Principal, Cincinnati Office
Jay Yuan, PhD, PE has been working in the packaging industry in the United States for 23 years. His expertise ranges from flexibles to rigid, and carton, corrugates, plastics to metal packages. He holds two patents for major brand name package designs currently on the market. The recent 28 oz Gatorade package co-development work with PepsiCo won the 2014 DuPont Packaging Award for the most responsible packaging. He received an M.S. in Solid Mechanics from Peking University and obtained his PhD. at the University of Akron. Dr. Yuan is a registered professional engineer and member of IoPP, ASME, SPE and TAPPI. He is a strong activist for in-silico transit testing in package development.
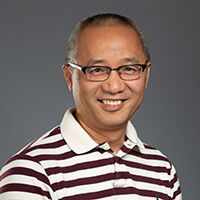
Sean Zhang, PhD – Staff Consultant, Cincinnati Office
Sean Zhang, PhD, has been working in the packaging industry in the United States for 12 years. He is a highly skilled & experienced modeling & simulation analyst in packaging, not only in using the commercial finite element software codes, but also in programming customized user-interface and automation routes. He received a M.S. degree in Applied Mechanics from Fudan University and obtained his PhD. at University of Rochester. Dr. Zhang is a member of ASME.
Leave a Comment
You must Register or Login to post a comment.