The New and Improved API 579 Standard *

Well, it’s been a while. The last version of API 579 was issued in 2007, so upgrades have been 9 years in the making. There are many small corrections and tweaks and a few big changes as well. I’ll walk through the most important of these.
Reorganization
The most conspicuous change in the 2016 edition may be the Table of Contents. Previously, most of the reference information required in the analyses was relegated to the many Annexes located in the back of the document. That’s where you would find the stress analysis techniques, fatigue analysis, material property data, and an array of valuable information. Now, every Annex has been repositions to appear after the Part to which it applies. For example, the reference stress solutions for crack-like flaws appear in Annex 9C (after Part 9), rather than in Annex D. No change in substance here…you just need to learn where to look.
Expanded Design Codes
At the very beginning of API 579, within the “Scope” section, ¶ 1.2.2, “Application Construction Codes” states:
“The assessment procedures in this Standard can be used for FFS assessments and/or rerating of equipment designed and constructed to the following [codes]”
The list of codes in this section is expanded to include several new additions, such as:
- 4, Pipeline Transportation Systems for Liquids and Slurries
- 8, Gas Transmission and Distribution Piping Systems
- 12, Hydrogen Piping and Pipelines
- API STD 650, Welded Tanks for Oil Storage
- API STD 620, Large Welded Low Pressure Storage Tanks
- API STD 530, Calculation of Heater-Tube Thickness in Petroleum Refining
The expansion of applicable codes is a good thing. It provides direct support for the use of API 579 in an expanded set of environments. This can be increasingly important when dealing with jurisdictions or if a failure winds up in the courts.
Fatigue Assessment
One of the big changes in 2016 is the addition of a new Part on fatigue assessment. But this may not be quite as big a change as it might seem since fatigue assessment was already included in Annex B1.5 of the 2007 edition.
One personal observation on the new Part 14 Level 2 assessment is that it involves a fairly complicated set of calculations. So there is likely to be a tendency for fatigue calculations to be performed primarily by specialists.
Partial Safety Factors in Flaw Assessment
One of the biggest changes is in the way the crack-like flaw assessment (Part 9) handles safety factors.
But first, what are partial safety factors? Traditional safety factors are applied at the end of a calculation. For example, consider the stress in a bar in bending, where σ=Mc/I. If we calculate the stress to be 10 ksi, and we want a safety factor of 3 on yield, we need a material with a yield stress of 30 ksi. That’s the application of a traditional, single, safety factor applied to the final calculated stress.
Partial safety factors (PSFs) are safety factors applied to several inputs of a calculation. For example, we might apply one safe factor to the moment, M and a different factor to the dimension, c. The selection of these safety factors is typically related to the uncertainty in the input parameter and in the acceptable probability of failure.
In the 2007 Level 2 assessment, partial safety factors were applied to three parameters: flaw size, material toughness, and stress. The user made choices and calculations related to the uncertainties and acceptable probability of failure. Once these selections were made, the PSFs were applied to the inputs, before the calculations were performed.
A reading of the 2016 Part 9, Level 2 procedure will reveal almost no reference to PSF. Closer reading introduces a few subtleties, but Annex 9A.1 provides the key insight.
“The uncertainty in the independent variables in a FAD analysis [may] be accounted for by choosing conservative estimates for each of these parameters. Alternatively, mean values of these parameters may be used with Partial Safety Factors.”
If conservative lower bound values are used for the input values in the assessment, PSFs are not needed (as they similarly were not need under the 2007 edition). If, on the other hand, mean values are used, PSFs remain appropriate.
The PSF section was pulled from the 2017 edition because of some problems, particularly with the PSF on stress. But, in my opinion, routinely ignoring the PSFs (i.e. setting all the PSF’s to 1) would be an error in most cases. Unfortunately, the 2016 version provides no guidance on what factors to use.
One final point: a sentence was added in 2016 to clarify the use of joint efficiencies. Specifically, use E=1 for stress calculations (paragraph 9.3.4.2). Remember, joint efficiency is a knock-down factor to account for overall weld quality. The fracture mechanics analysis is explicitly evaluating the flaw. Inclusion of E<1 in stress calculations is double-dipping.
Remaining Strength Factors
Annex 2F is now included to provide some guidance on establishing Remaining Strength Factors (RSFs). This section discusses the differences in the Burst Pressure Ratio (i.e. burst pressure/MAWP) from different codes. If a constant burst pressure ratio is adopted, different construction codes will have different RSFs.
Modification to RSF may also be based on other factors such as loading or consequence of failure.
Component “Type” Definition
Part 5 of the 2016 version carves out a simpler (and more restrictive) definition of a Type A component and uses that to provide and a simpler Level 1 local thin area assessment procedure.
The following Table provides a summary of the component type definitions in 2007 and 2016.
Additional guidance on the more restrictive 2016 Type A component rules is also provided in API Figures 4.3 – 4.5, which deal with towers and vessels with saddles.
This change provides a somewhat simpler Level 1 procedure which eliminated the Tensile Stress Factor (TSF) in evaluating the circumferential extent of cylindrical shells, conical shells, and elbows.
Metallurgical Investigation of Fire Damage
A new Annex 11B is included to provide guidance on the use of metallurgical techniques in the assessment of fire damage. This annex provides guidelines for both performing a metallurgical investigation and interpreting the results. It is limited to carbon, low alloy, and stainless steels.
I think that this annex can be considered an overview and introduction to metallurgical techniques for the non-metallurgists. It addresses a wide range of topics including both field & laboratory techniques.
Another section on the interpretation of test results (paragraph 11B.8) provides insight into, for example, the implications of increases or decreases in the tensile stress, and the potential for sensitization.
Taken as a whole, this section may provide significant insight, particularly to an inexperienced non-metallurgical engineer.
Creep Assessment
While the basic remaining life calculation methodology is unchanged, there have been several changes to the creep procedure of Part 10. Most notably, the allowable creep damage fraction has been changed from Dcallow = 0.8 (2007) to Dcallow = 1 in 2016 (see Equation 10.28).
Residual Stress
The residual stress section has been the subject of substantial work since the release of the 2007 edition. This has been prompted by recent improvements in the simulation of weld residual stress, which provides an opportunity for improvement.
Typically the calculations in this Annex are “behind the scenes”, incorporated into the residual stress calculators used in Signal FFS® or similar software. This revision includes changes in equations and calculations, a greater emphasis on heat input, and numerous other changes, but the average user may not directly interact with this annex in great depth.
Conclusion
There are many, many other small changes throughout, some just editorial and some substantial, but I believe this brief summary covers the most important. If you have done extensive work with the 2007 version, I’d recommend you carefully review your procedures and spreadsheets when working with the new version. Many small changes are present throughout.
API 579-1 / ASME FFS-1 Workshop
If you would like to learn more on this topic, I will be holding a workshop on fitness-for-service evaluation methods of the API 579-1/ASME FFS-1 (2016) Standard…including the many new additions and changes in the 2016 edition. The workshop will be held September 19 – 22, 2017 in New Orleans, LA. For more information, and to register, go to https://www.stress.com/event/api579.
* as appeared in Stress Talk 2017
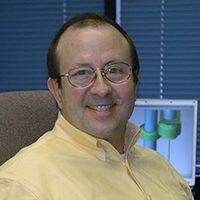
Greg Garic, PE – Principal, New Orleans Office
Greg Garic has over thirty-five years of experience in analysis and fitness-for service assessment. He has spent most of his career working in the areas of structural integrity assessment and remaining life evaluation of pressure vessels and piping. He has served as a member of numerous ASME Committees, Subcommittee, and Task Groups. He is also an associate editor of several PVP volumes relating to fracture mechanics and fitness-for-service issues.
Leave a Comment
You must Register or Login to post a comment.